Así es la tecnología que ayudó a Zalando a afrontar el crecimiento de la demanda
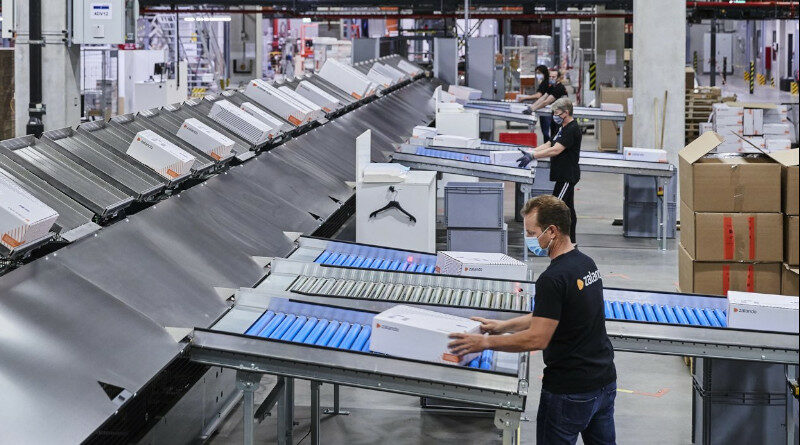
En la pasada primavera, coincidiendo con la primera ola de coronavirus, Zalando instaló en su centro de Erfurt un sistema capaz de clasificar hasta 4.800 pedidos por hora.
El impulso otorgado al ecommerce por la pandemia de coronavirus se ha visto reflejado en los resultados de Zalando en el último año, al experimentar un crecimiento de doble dígito en sus ventas. Un 27% y un 29,9% de alza en el segundo y tercer trimestre, respectivamente.
El crecimiento de la demanda online ante la imposibilidad de acudir a la tienda física por las restricciones a la movilidad para frenar la pandemia – y por seguridad, en las etapas en las que se ha podido asistir- ha obligado al marketplace alemán a adaptar la tecnología de sus almacenes y poder hacer frente a dicho incremento.
Entre las nuevas tecnologías adoptadas para afrontar tal reto durante 2020, Zalando instaló en su centro logístico de la ciudad alemana de Erfurt, un sistema de clasificación y envío de artículos diseñado para espacios muy reducidos.
El sistema Denisort Compact de la empresa suiza Ferag AG fue la plataforma elegida, ya que sus bandejas permitían al ecommerce procesar cada hora hasta un total de 4.800 pedidos de diferentes formas y tamaños. Con este sistema, la compañía lograba agilizar el proceso de clasificación de paquetes hacia destinos de envíos adicionales.
Con una longitud de 31 metros y equipado con 18 rampas de salida, el sistema intralogístico se utiliza en las actividades de envío para la clasificación precisa de artículos etiquetados hacia diferentes destinos, por país o código postal. Cuenta con un diseño modular, que facilita su instalación en cualquier punto del almacén, y un clasificador vertical y automático que, además de configurarse con rapidez, puede adaptarse a otros procesos o a un incremento de la producción.
Por el momento, los artículos se depositan en el sistema clasificador de forma manual, aunque en el futuro, Zalando planea que se puedan depositar en el sistema vía inducción completamente automática. Los empleados colocan los paquetes etiquetados y preparados para su envío en las bandejas del clasificador. Tras su escaneo y asignación de destino automáticos, estos se desplazan hacia la rampa asignada. A partir de ahí, un miembro del personal va a buscarlos y los apila en palés que luego se llevan a las puertas de salida con carretillas elevadoras y se cargan en los camiones para su distribución.
Puesto en marcha la pasada primavera, las primeras operaciones del sistema coincidieron con el momento en que se disparó el número de pedidos como consecuencia de la crisis sanitaria. Los buenos resultados cosechados han incentivado a la firma alemana a instalar este sistema en el centro de distribución que tiene en Mönchengladbach.